
Ball mill - Wikipedia
A ball mill is a type of grinder used to grind, blend and sometimes for mixing of materials for use in mineral dressing processes, paints, pyrotechnics, ceramics, and selective laser sintering. It works on the principle of impact and attrition: size reduction is done by impact as the balls drop from near the top of the shell. A ball mill consists of a hollow cylindrical shell rotating about ...
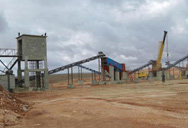
Sponenburgh Ball Mill Part3: Melting Metal - …
10.12.2015 · Melting lead and aluminum for ball mill media in another YouTube invention- the hole-in-the-ground forge. We dug a 3ft hole in the ground anout …

melting production line Tonga
melting production line Tonga. Melting Urea an advances technology was widely used in the world Melting Urea technology allows production of NPK compound fertilizers with a high nitrogen content which overcome the disadvantages of current popular technologies low rate of Nitrogen and lower nutritional content

The effect of ball milling on the melting behavior …
It was found that the lowest melting point was achieved at 213.6°C for Sn-3.5Ag-3nanoCu produced by ball milling. The wetting angle deterioted as Cu nanoparticles were added into the Sn-3.5Ag ...

Application of the combination of ball-milling …
The aim of the study was to develop an amorphous solid dispersion of a poorly water-soluble drug with high melting point by ball milling and hot melt extrusion as a co-processing method. Solid dispersion systems were prepared by ball milling-hot melt extrusion and then compared with those prepared with hot melt extrusion. The effects of three process parameters in the co-processing method ...
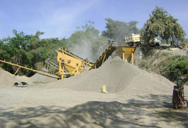
The effect of ball milling on the melting behavior …
Pulverisette ball mill (P7) and Vibratory ball mills are used to carry out the milling of the powders at room temperature and at lower temperatures (−104 °C), respectively. We report a relatively smaller depression of melting point ranging up to 5 °C with respect to original alloys. The minimum stone sizes achieved and the depression of ...

Fabrication of Mn-Bi Nanoparticles by High Energy Ball Milling
arc-melting” and “without arc-melting”, respectively. The coarse powder was then milled on a SPEX 8000D high energy ball mill for various time of 0.258h in different environments of Argon ...

Characterisation and milling time optimisation of ...
melting (SLM). Previous research has indicated that powders suitable for SLM include milled nanocrystalline aluminium powders with an average stone size of 60 nm and good flowability (Carr index less than 15 %). This study employs advanced nanometrology methods and analytical techniques to investigate the powder morphology, phase identification, average stone size and flowability of ball ...

Ball Mill - RETSCH - powerful grinding and …
The High Energy Ball Mill E max and MM 500 were developed for grinding with the highest energy input. The innovative design of both, the mills and the grinding jars, allows for continuous grinding down to the nano range in the shortest amount of time - with only minor warming effects. These ball mills are also suitable for mechano chemistry. Mixer Mills grind and homogenize small sample ...

High energy ball milling process for nanomaterial …
The ball mill system consists of one turn disc (turn table) and two or four bowls. The turn disc rotates in one direction while the bowls rotate in the opposite direction. The centrifugal forces, created by the rotation of the bowl around its own axis together with the rotation of the turn disc, are applied to the powder mixture and milling balls in the bowl. The powder mixture is fractured ...

Synthesis and characterisation of advanced ball …
01.09.2016 · High-energy ball-milling employed to synthesise Al-Al 2 O 3 nan-composite powders. • The effect of the milling and pause duration analysed. • The characteristics of the composite powders examined. • The effect on the powders micro-hardness analysed. Abstract. Selective laser melting (SLM) offers significant potential for the manufacture of the advanced complex-shaped aluminium …

Tungsten Carbide Milling Ball (3~10mm diam.), …
Table-top Planetary Ball Mill with Four SS Milling Jars (4x100ml) - MSK-SFM-1S Sale Price: RFQ Planetary Ball Mill(4x500ml Capacity) with four Nylon Jars & Lock Clamps up to 37G - MSK-SFM-1

Melting behavior and origin of strain in ball …
Ball-milling was carried out for different milling times ranging from 45 min to 32 days. The milling time dependence of the average grain-size and of the density of lattice defects, mainly dislocations, were determined by the modified Williamson-Hall and Warren-Averbach procedures based on the dislocation model of mean square strain. Characteristic stone sizes of ball-milled Al-powders ...
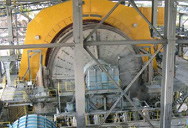
Dioxins reformation and destruction ... - Scientific …
15.03.2016 · Milling tests were carried out in a planetary ball mill (XMQ-0.4L, Kexi, China), at 275 rpm (jar-to-planetary disk rotation speed ratio was equal to −2); 180 g stainless steel balls (Ø 5 mm ...

Ball Milling | Material Milling, Jet Milling - AVEKA
Ball milling is a size reduction technique that uses media in a rotating cylindrical chamber to mill materials to a fine powder. As the chamber rotates, the media is lifted up on the rising side and then cascades down from near the top of the chamber. With this motion, the particles in between the media and chamber walls are reduced in size by both impact and abrasion. In ball milling, the ...

Melting point depression and microstructure in …
Ball-milling was carded out for different milling times ranging from 45 min to 32 days. The milling time dependence of the average grain-size and of the density of lattice defects, mainly dislocations, were determined by the modified Williamson-Hall and Warren-Averbach procedures based on the dislocation model of mean square strain. Evolution of the average grain-size and microstructure has ...

Royal Duyvis Wiener B.V. – from cocoa to chocolate
Royal Duyvis Wiener B.V., founded in 1885 with its head office in Koog aan de Zaan, the Netherlands, is one of the leading manufacturers in the global cocoa and chocolate processing industry.

Characteristics of the Ti1.27Fe + 11 wt.% Ni …
The Ti 1.27 Fe + 11 wt.% Ni composite synthesized by arc melting and ball milling and its possible use in hydrogen storage were studied. First the intermetallic Ti 1.27 Fe was obtained from elemental powders of Ti and Fe by using the arc melting in argon atmosphere and was cracked in a reactor, after that nickel powder was added to the Ti<sub>1.27</sub>Fe alloy before the milling.

MSE Supplies LLC - Advanced Materials and Lab …
MSE Supplies is a trusted scientific supplier of high-quality crystal substrates, sputtering targets, lithium battery materials, graphene, ITO and FTO substrates, milling equipment, jars & milling media, shakers, mixers & lab equipment, and analytical services for research and manufacturing. We Enable Innovations.