
Centerless grinding - Wikipedia
Centerless grinding is a machining process that uses abrasive cutting to remove material from a workpiece. Centerless grinding differs from centered grinding operations in that no spindle or fixture is used to locate and secure the workpiece; the workpiece is secured between two rotary grinding wheels, and the speed of their rotation relative to each other determines the rate at which material ...

Plunge Grinding or In-feed Centerless Grinding - …
Plunge, or In-feed grinding is a method of centerless grinding that has been used by operators in grinding relatively complex parts. Unlike the through-feed grinding process which pulls the workpiece past the grinding wheels, the workpiece in in-feed is held and supported between the wheels for a thorough grinding even in the smallest part diameters.

What is Creep Feed Grinding and how does it work ...
Creep feed grinding achieves significantly higher productivity in mass production compared to reciprocating grinding. With todays conventional, highly porous grinding wheels, very high material removal rates are achieved with creep feed grinding. The wheel wear is typically lower than in reciprocating grinding. The surface quality is typically ...

What is Thru Feed Grinding? | Lapmaster Wolters
Thru-Feed Grinding is a production flat machining process that does almost everything a conventional double disc or vertical spindle grinder can do. Thru-feed grinding is the most efficient method known for high production surface grinding of small to mid size parts …

Infeed Grinding | TGS Centerless Grinders
Infeed Grinding. Infeed centerless grinding is used to grind parts that require multiple diameters and profiles to be ground at one time. The part is loaded onto the blade and pushed against a stop to hold it stationary. With the necessary form dressed into the grinding wheel and the regulating wheel, the grinding wheel is fed into a specified ...

TYPES OF GRINDING PROCESS - Mechanical …
Through feed grinding process is considered as quite productive as grinding process could be performed simultaneously for number of objects. In-feed grinding If we have a workpiece, which has not exactly not right circular cylindrical shape, in this situation we will prefer in-feed grinding process as grinding wheel could be dressed according to the workpiece surface.

Differences Between Thru-Feed And In-Feed Grinding
At Sturdy Grinding in New Haven, MI, we use through-feed grinding techniques to provide high-quality products and increased productivity for your company. Thru-feed vs. In-Feed Grinding. Thru-feed grinding is a type of centerless grinding. During this process, …

Grinding Parameters and their Effects on the Quality of ...
before grinding process. Balance (2) (made in Japan, model CG-12K, measuring range of 0-12 kg ± 0.001 kg). It was used to determine the mass of the ground grains after grinding process (samples 200 g). stone moisture tester (made in Japan, model PM 300 and accuracy 0.2- ± 0.5%) It is used to record moisture content for grains. Standard testing

Creep-feed Grinding Is A Milling Process | Modern …
Creep-feed grinding is an abrasive machining process, but beyond that, it doesn’t resemble other forms of grinding. Nelson Beaulieu, grinding product manager with Hardinge Inc., says it makes more sense to characterize creep-feed grinding as a milling process.

Grinding Parameters | SpringerLink
25-05-2018 · The basic process parameters in grinding processes are the cutting speed v c, the feed velocity v f, the depth of cut a e, and the width of cut a p (see Fig. 1, see also Denkena and Tönshoff 2011).The cutting speed is in general equal to the circumferential speed of the grinding wheel.

Chapter 18. Feed Milling Processes
Grinding also increases the total surface area of a given weight of feed, thereby allowing more space for steam condensation during the conditioning process. This results in a higher feed temperature and more water absorption which together, within the time available, increases gelatinization of raw starch.
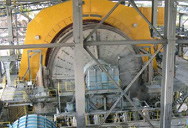
Post-Pre grinding - Van Aarsen | The vital link to …
The GD and 2D hammer mills are designed for the animal feed industry, to grind raw materials into small particles and meal. Both the GD and 2D hammer mill series cover capacities ranging from 5 – 100 tons per hour, dependent on type of raw material, formula and required grinding structure and can be incorporated in a pre-grinding as well as a post grinding system as a complete grinding ...
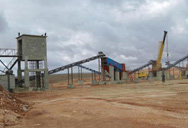
Grinding Machining Process : Complete Notes - …
The grinding process has the least material removal rate among other machining processes because of the following reasons- Size effect: As above discussed the machining is done by the abrasive action of grinding wheel that’s why a large portion of the abrasive will be embedded inside the wheel and a small portion of abrasive will be allowed to interact with them , therefore, less material is ...

In-feed Grinding - Centerless grinding, tight …
In-Feed centerless grinding is available for parts that have shoulders or obstructions not allowing them to pass in between both the regulating and grinding wheels. We have the capability to hold tight tolerances and ensure critical features are met per customer specification.

In-feed centerless grinding | Find suppliers, …
Home / Processes / Chip breaking / Grinding / Centerless grinding / In-feed centerless grinding. In-feed centerless grinding . Abrasive treatment where the workpiece is first placed in its working position, and a grinding wheel is then applied radially against the workpiece. ... Take this process!

Grinding (Machining) - an overview | ScienceDirect …
In ECG, generally the direction of wheel rotation is opposite to the direction of feed of workpiece. The contact area between wheel and workpiece is larger in EC face grinding process, hence it is a faster process. As the contact area is less, EC cylindrical grinding is a slower process. Typical values of ECG operating parameters are given as ...

What Is End Feed Grinding?
End-feed grinding, specifically, is a method that is good for shaping a piece of metal so that one end is larger than the other. When a piece of work is inserted between the two wheels, it is also positioned between a third piece that is called a work rest.

What is Thru Feed Grinding? | Precision Surfacing …
Thru-Feed Grinding is a production flat machining process that does almost everything a conventional double disc or vertical spindle grinder can do. Thru-feed grinding is the most efficient method known for high production surface grinding of small to mid size parts …