
Reduce Consumption Of Cement
Cement ratio raw mill 15 23.2 17.4 22.6 coal mill 25 4.1 3.1 4.0 pyro system 26 26 19.5 25.6 cement mill 27 27.0 35.1 other 10 8.0 14.8 total 75 100 grinding tech improvement play the most important role to reduce power consumption sum power consumption of grinding section 47.5kwht.Cement, 62 of total power consumption decrease power.

Reduce Consumption Of Cement- DYNAMIC …
Limestone based cement reduces energy consumption and co2 production by 97 percent in contrast to ordinary portland cement drexels cement is made of up to 68 percent unfired limestone a plentiful cheap and lowcarbon dioxide resource american society for testing and materials standards for portland cement limit the amount to 5 percent. More Details Use Of Water Reducers Retarders And ...
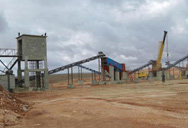
Cement Manufacturing: Ways to Reduce CO2 …
Over the last thirty years, the specific fuel consumption of cement manufacturing has decreased by 40%, which directly reduces the CO2 emission by the same magnitude. Furthermore, coal, which is conventionally used for combustion, is increasingly being replaced by alternative fuels like Municipal solid waste (MSW), stone tires, dried sewage sludge, etc.

Reduce Consumption Of Cement - …
Reduce Consumption Of Cement. The main potential in reducing energy consumption and CO 2 emissions from cementconcrete production is in improvement of cement pyroprocessing Pyroprocessing transforms the raw mix into clinkers At present about 78 of Europes cement production is from dry process kilns a further 16 of production is accounted for by semidry and semiwet process kilns with the ...

Reduce Consumption Of Cement
Reduce consumption of cement - Crusher Unit. Cement , industrial efficiency technology & measures. greening cement production has a big role to play in reducing next to water, concrete is the second-most ... Read more. reduce consumption of cement. reduce consumption of cement, Besides the ordinary crushing & grinding machines, mining equipments also include many very professional machines ...

Reduce Energy Consumption: Cement Production …
14.03.2020 · Energy savings can be generated by optimizing the combustion process, controlling temperature profiles, optimizing the heat recuperation process, and others. On average, MPC systems allow cement plants to reduce their energy consumption by 3% to 5%, as well as provide better product quality and capacity improvements.

reduce consumption of cement - davyroelstraete.be
The main potential in reducing energy consumption and CO 2 emissions from cement/concrete production is in improvement of cement pyroprocessing. Pyroprocessing transforms the raw mix into clinkers. At present, about 78% of Europes cement production is from dry process kilns, a further 16% of production is accounted for by semi-dry and semi-wet process kilns, with the remainder of European ...

Autopilot of Cement Plants for Reduction of Fuel ...
cement production that can help reduce fuel consumption and emissions. The system is robust to concept drift and fault-tolerant to unexpected sensor malfunctions encoun-tered during real operations, and was tested and verified in real-world cement plants. Our system is generalized enough to be quickly adapted to other use cases within the cement

reduce consumption of cement - johannsoutdoor.nl
reduce consumption of cement; share . stone Admixtures - cementorg. Superplasticizers, also known as plasticizers or high-range water reducers (HRWR), reduce water content by 12 to 30 percent and can be added to concrete with a low-to-normal slump and water-cement ratio to make high-slump flowing concrete Flowing concrete is a highly fluid but workable concrete that can be placed with ...

Best energy consumption - International Cement …
The benefit of aids on cement flowability has to be considered, along with the added scope for reduction of cement clinker content with some modern additives. Correct timing on the maintenance of a first chamber cement mill lining and the successful implementation of an expert system on a cement mill both offer benefits in terms of power consumption (see case studies panel). Accurate process …

Energy efficiency in cement manufacture - VDZ
Following a considerable reduction to a level of around 99 kWh in 2008, the specific electricity consumption has increased again: in 2018, an average of 111 kWh was required per tonne of cement; this corresponded to absolute consumption of around 3.78 TWh. The increase in electricity consumption in the years following 2008 has various reasons. These include increasing demand …

Reduction of Energy Consumption in Cement …
The present study investigates the possibility of introducing zinc oxide nanoparticles into the cement raw mix so as to reduce the energy consumption and CO 2 emissions during processing. Zinc oxide nanoparticles are prepared via a hydrothermal growth method using zinc acetate dihydrate and sodium hydroxide as precursors. The percentages of zinc oxide nanopowder added to the cement raw material was varied between 1% and 3%. The resulted clinker and cement …

Engineering sustainable and durable concrete to …
a reduced demand for cement, as waste by-products from other industries such as slag, fly ash, and silica fume are used within SFRC and inherently emit very low levels of carbon dioxide. Most importantly, carbon dioxide emissions from the production of SFRC with fly ash and/or slag as cementitious replacements are reduced by a remarkable 60-70 per cent compared to traditional reinforced …

CEMENT INDUSTRY - The Energy and Resources Institute
dependence on imports and reduces the cost of construction. It also enables further development ofthe economy through improved infrastructure. In the case of some countries it is even possible to show strong positive correlation between GDP and cement consumption over time. Cement Industry Trends Report As per one of the UN 2014 report, majority of the 2.5 billion new urban inhabitants ...

Control Engineering | Reduce Energy …
On average, MPC systems allow cement plants to reduce their energy consumption by 3% to 5%, as well as provide better product quality and capacity improvements. Energy management profit Armed with optimized production information, manufacturers can then project, in advance, how much energy will be required for similar loads or batches.

CO REDUCTION IN THE CEMENT INDUSTRY
The efforts of the cement industry to reduce climatically relevant emissions are thus confined to carbon dioxide. By way of example, Figure 3 shows the specific CO 2 emissions from the German cement industry in the period from 1990 to 2001, subdivided into direct emissions (from fossil fuels and limestone calcination) and indirect emissions due to power consumption. Secondary fuels are not ...

Energy Efficiency and CO 2 Reduction in the Cement Industry
As cement manufacture is a mature tech- nology, no breakthrough technologies are foreseen that will reduce thermal energy consumption to any significant extent. Car- bon capture and storage (CCS) may be a viable option to reduce CO2emissions from World cement production by region, evolution 2001-2012 Index 2001 = 100

reduce consumption of cement - …
cement industry needs to use the most efficient technologies to safeguard its future. To be profitable, cement producers need to: − Increase availability of equipment and reduce downtime − Lower maintenance costs − Reduce energy consumption per ton of produced cement Achieving high levels of efficiency and availability will increase

Cement - Wikipedia
Cement consumption levels for this region fell by 1.9% in 2010 to 445 Mt, recovered by 4.9% in 2011, then dipped again by 1.1% in 2012. The performance in the rest of the world, which includes many emerging economies in Asia, Africa and Latin America and representing some 1020 Mt cement demand in 2010, was positive and more than offset the declines in North America and Europe. Annual ...

Cement - keralaenergy.gov.in
Cement is an essential part of our daily lives Cement production contributes significantly to annual anthropogenic global CO 2 emissions, mainly because such vast quantities are used. Thus, energy efficiency becomes very important in its production to reduce this carbon footprint.