
The Latest Developments in Iron Ore Processing
• Fines Jigs hard to control • ‘Over the bed’Jigs • ‘Through the bed’Jigs –Ragging • Capacity –85t/h per meter width of jig to max of 4m wide jig Jigging on Iron Ore

Beneficiation of Iron Ores – IspatGuru
Several methods/techniques such as washing, jigging, magnetic separation, gravity separation, and flotation etc. are used to enhance the Fe content of the Iron ore and to reduce its gangue content. These techniques are used in various combinations for the beneficiation of iron ores. For beneficiation of a particular iron ore the emphasis is usually to develop a cost effective flow sheet incorporating necessary crushing, grinding, screening and beneficiating techniques …

Iron Ore - an overview | ScienceDirect Topics
To make fluxed sinter, fine-sized ore is first mixed with coke and fluxes, and heated in a sinter plant. Sinter process agglomerate iron ore, dust, or fines with other fine materials at high temperature to create a product that can be used in the BF. This process has a continuous moving belt on which the coke is ignited.

Iron ore pelletizing systems - liming
The iron is usually ground to a very fine level and mixed with limestone or dolomite as a fluxing agent and bentonite or organic binders as a binding agent. If the ore is a Hematite ore, coke or anthracite coal can be added to the mix to work as an internal fuel to help fire the pellets. This mixture is blended together in a mixer and fed to balling discs or drums to produce green …

Iron Ore Agglomeration Processes and their …
Briquetting is the simplest and earliest applied process. Fine grained iron ores are pressed in to pillow shaped briquettes with the addition of some water or some other binder under high mechanical compressive pressure. In the nodulizing process, fines or concentrate along with carbonaceous material are passed through inclined rotary kiln heated by gas or oil. The temperature inside the kiln is sufficient to soften but not high enough to fuse the ore…

Iron Ore Pelletizing Process: An Overview | …
10.07.2017 · The iron ore pelletizing process consists of three main steps: Pelletizing feed preparation and mixing: the raw material (iron ore concentrate, additives—anthracite, dolomite—and binders are prepared in terms of particle size and stone specifications, dosed, and mixed together to feed the pelletizing process;

Iron Ore - an overview | ScienceDirect Topics
Iron ore fines are characterized on a physical basis by variations in particle size, shape, density, porosity, surface area, roughness, and wettability. Furui et al. (1977) divided iron ore particles into nucleus particles of + 0.7 mm size, intermediate particles of − 0.7 + 0.2 mm size, and adhering particles of − 0.2 mm size.

Direct reduced iron - Wikipedia
07.10.2005 · Direct reduced iron (DRI), also called sponge iron, is produced from the direct reduction of iron ore (in the form of lumps, pellets, or fines) to iron by a reducing gas or elemental carbon produced from natural gas or coal.Many ores are suitable for direct reduction. Direct reduction refers to solid-state processes which reduce iron oxides to metallic iron at …
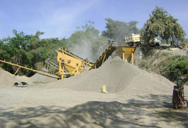
Iron ore - Wikipedia
09.11.2002 · Lower-grade sources of iron ore generally require beneficiation, using techniques like crushing, milling, gravity or heavy media separation, screening, and silica froth flotation to improve the concentration of the ore and remove impurities. The results, high-quality fine ore powders, are known as fines.

iron ore fines - Deutsch-Übersetzung – Linguee Wörterbuch
Sintering is a process whereby iron ore fines are heated in a mixture of fluxes in order to agglomerate the particles into larger-sized pieces. iea.org Beim S intern wird das Feinerz in einem Zuschlagstoffgemisch erwärmt, um die Partikel zu größeren Agglomeraten zu verschmelzen ("stückig zu machen").

IRON ORE PELLET PLANT IMPORTANT PART - …
06.12.2017 · Lower-grade sources of iron ore generally require beneficiation, using techniques like crushing, milling, gravity or heavy media separation, screening, and silica froth flotation to …

Characterization and Beneficiation of Dry Iron …
18.09.2018 · Characterization and beneficiation of dry iron ore processing plant reject fines of Khondbond region, India, was investigated. Different characterization techniques viz. size analysis, size-wise stone and density analysis, X-ray diffraction analysis, sink-float analysis, thermo gravimetric analysis, scanning electron microscopy, and QEMSCAN were carried out.

Iron Ore Beneficiation Plant Cost
Iron Ore Beneficiation Plant Cost, Iron Ore . Alibaba offers 151 iron ore beneficiation plant cost products. About 36% of these are mineral separator, 4% are other mining machines, and 2% are mine mill. A wide variety of iron ore beneficiation plant cost options are available to you, such as magnetic separator, flotation separator, and

iron ore beneficiation processing plant line
Iron Ore Processing Plants - Iron Ore Wash Plants - CDE CDE iron ore processing plants reduce alumina and silica contamination and increase efficiencies in steel production. Learn more about our custom modular iron ore beneficiation washing processing plants today. ... P-Line Inclined Screens. Innovative Technique to generate saleable Iron Ore Fines from Ore Fines from beneficiation plant ...